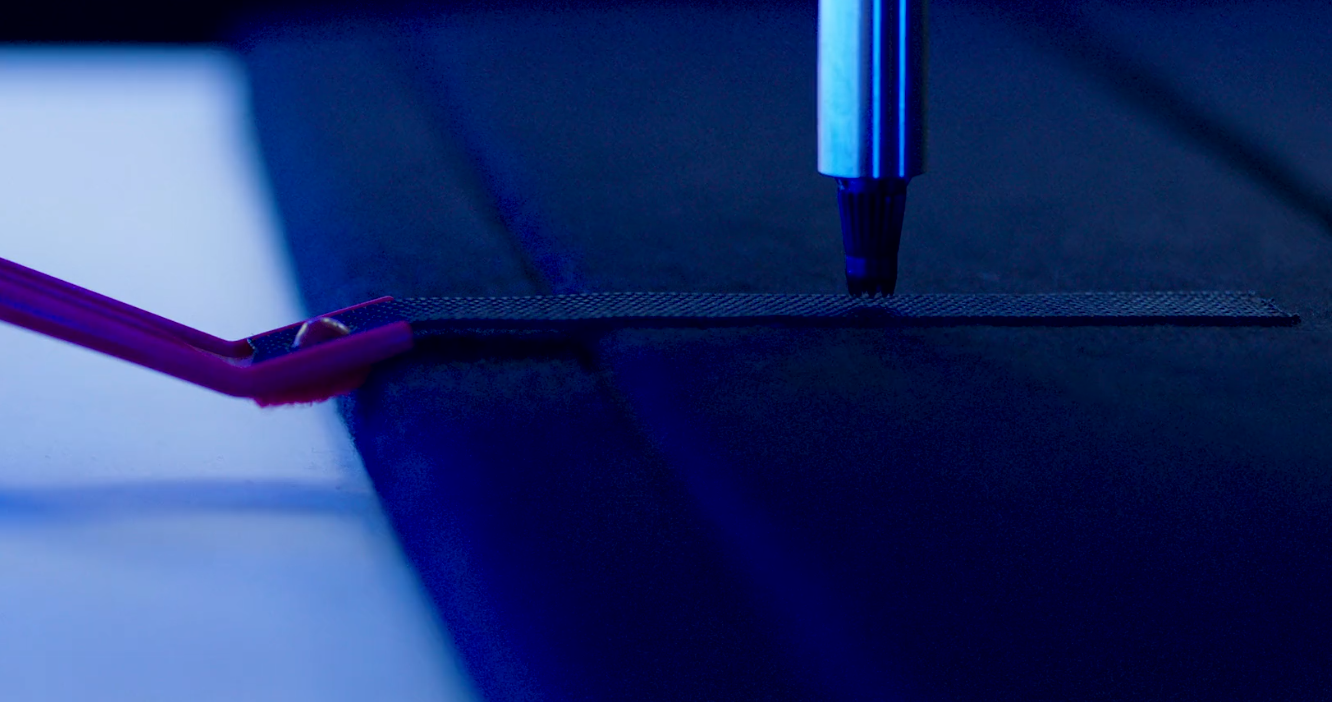
LightWWeight connection for sandwich panel
In this project, MultiMaterial-Welding collaborated with KVT Fastening and the University of Applied Sciences Northwestern Switzerland, to apply the MM-Welding technology to interior automotive parts and to develop the process understanding and development methods, to adapt the technology to several applications in the transport area.
The scope of the project is to apply the MM-Welding technology to interior automotive parts (honeycomb-core boards typically used for trunk floor or parcel shelf) and to develop the process understanding and development methods to adapt the technology to several applications in the transport area.
The developed innovation in the project is a mechanism-based understanding of the process, based on four elements:
- Material characterization and constitutive modelling of the viscoelastic thermomechanical behavior
- Development of a testbed including online process monitoring for detailed process analysis
- Development of knowledge based methods to understand the behavior of the ultrasonic excitation and predict the viscoelastic thermomechanical behavior in the joining area
- Fast design methods to apply the MM-Welding technology by first time right to several applications
Facts & figures
Consortium:
- Multi-Material Welding
- KVT Fastening
- University of Applied Science Northwestern Switzerland
Funding:
Innosuisse
Budget:
1.16 mio. CHF
Whitepapers:
- Zweifel et al, Experimental and Numerical Development of Multi-Material Joining Technology for Sandwich-Structured Composite Materials,. Materials 2021, 14,6005
- Brauner et al., Joining of multi-material assemblies by the MultiMaterial-Welding technology, Proceeding of ITHEC 2018, Bremen
- Zur Einheit Verschmolzen, Carbon Composites Magazin, 1/2019, p39
Highlighted results
Full process modelling
Intensive material characterization and advance dynamic modelling method lead to a complete FE model, providing a prediction of the process parameters (Load, temperature ...)
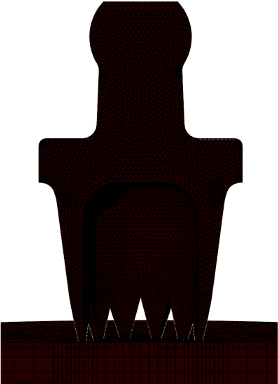
Online process monitoring
High speed camera in combination with DIC and Acoustic Emission allowed to fully characterize the process phases thanks to high acquisition rates. Tomography was used to assess and investigate the internal structure of the assembly.
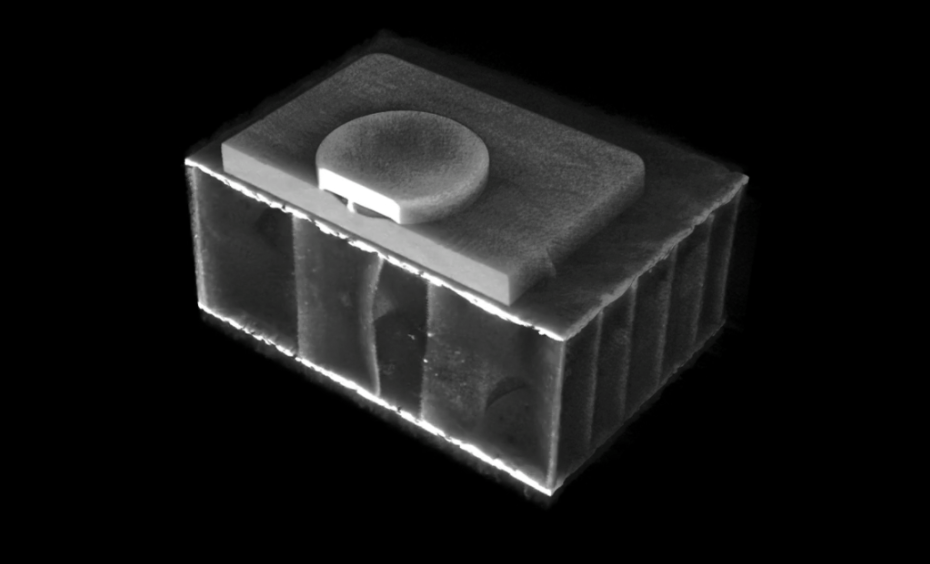
FEM as a support for an optimized design
Modal, Frequency response and impact models were used as tools to optimize the design of the fastener. This speeds up the development process as fewer physical prototypes need to be manufactured and tested.
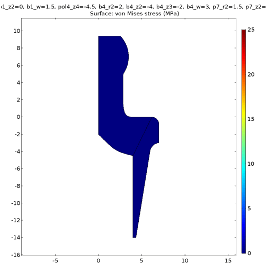
Want to collaborate with us?
We are always looking for new partners to work on R&D projects.
We’d be happy to talk about it.
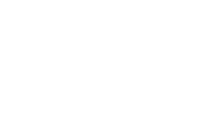